TL;DR
Welding Defect Rate Analysis &Rectification Using Six SIGMA Method:Dan FMEA at PT XYZ
ABSTRACT
In order to achieve the company quality objectives and to promote PT XYZ to be the world leading fabricator which produces its products safely, with quality, and meeting the customer’s requirements while remaining competitive, therefore, PT XYZ tries hard to implement zero defect system in its welding production. PT XYZ has monitored the welding defect rate and tried to reduce that rate. To minimize the defect rate down to zero defect, PT XYZ implements Six Sigma method in its welding production system, exercises systematic welding production and implements FMEA (Failure Mode and Effect Analysis) method in order to reduce failure risk in its welding production. The combination of both systems or methods, i.e. between Six Sigma and FMEA above, when synergically implemented would give promising results in the potential reduction of weld defect rate and in achieving of a good quality condition which is product free from failures or zero defect and achieving quality objectives as well as maintaining their customers.
Keywords:FMEA, Management System, Six Sigma, Zero defect,
INTRODUCTION
The industrial growth in the world manufacturing and fabrication industries are increasing rapidly, therefore, this will make companies compete with their competitors and amidst their competitors in the vast growth product technology and operations. The most important factor that the company needs to achieve is to secure their profit, which is gained from their products either goods or services. Achievement to improve effectiveness and efficiency in operations as well financing will be baseline performance that a company needs to achieve and to survive as well as gaining its prosperity.
There are some steps that need to be made by the company management in order to achieve their goals and objectives i.e. to develop strategies and improve the customer's loyalty towards the company products. Though this will mean that the company needs to improve their product quality and shorten their lead time when required. The focus on quality and well as customers will give positive influence to company business and especially to the company gross revenue and financial income.
Based on the production system exercised by PT XYZ, there are still some issues that influence the quality outcomes of their products and one of them is high repair rate issues in the welding production. Therefore, in minimizing or even eliminating the defects in the weld is something that the company should put an effort to in order to improve the products quality and maintaining their customers. The performance itself is a result which needs to be achieved by the company and according to Ratnasari [4] the improvement of company performance can be arranged by managing the workers or manpower resources, this exercise will be implemented through good recruitment, education, and training of the employees. The improvement of workers’ performances will be a continual exercise which gradually improves the company performance as well. The problem which continuously incurs on the production will adversely have an impact on the customer’s satisfaction and eventually to the company sales and revenue. Therefore improvement steps shall involve very core management and cooperation of all company personnel. The high weld defect rate which was exceeding the intended KPI (Key Performance Indicator) will alert the company for systematic mitigation and immediate resolution which need to be done on the production system, especially in the welding department.
Six Sigma and FMEA methods or approaches when implemented can be the best tools to discover what are the real root causes of the problems of increasing defects rate and how to confine the problems or mitigating them and to achieve normal lean operation. Six Sigma can be the controlling instrument which has a focus on the customer’s satisfaction, the higher Sigma level target is the higher company performance will be [6].
Based on that specified background as described above, the writer raised this issue of an article in his research which aims to the problem of how to minimize or eliminate the high welding defect rates of welding operations during in-process inspections and to prepare welds as the outputs in meeting the targetted KPI requirements, to achieve lean manufacturing and on time delivery project.
LITERATURE REVIEW
What is Six Sigma
According to Montgomery that at the beginning there were two types of Six Sigma models or operations used in the industry i.e. Motorola Six Sigma model or program dan Quality Six Sigma program. Motorola Six Sigma program was developed by Motorola in the year 1980’s using normal distribution curve (see Figure 1), while quality Sig Sigma program also used normal distribution curve but with the average value shifted by ± 1.5 from the target (see Figure 2). Motorola Six Sigma program reaches the limit down to 2 parts per billion defectives (0.002 ppm defects) while quality Six Sigma program is calculated only to 3.4 per million defects (3.4 ppm defects). [1]
Figure 1. Motorola Six Sigma Program
Figure 2. Quality Six Sigma Program
According to Pande that Six Sigma means almost the achievement of perfect goal or objective to satisfy customer requirements. Six Sigma is a method or technique to control and improve the quality systematically and serves as a new approach in the quality management system. Moreover, Pande stipulated regarding the five steps in implementing Six Sigma concept which are:
1) Identifying core processes and key customers,
2) Establish customer’s requirements,
3) Measure baseline performance,
4) Prioritize, analyze, and implement improvement,
5) Arrange processes for Six Sigma performances. [3]
Syukron also later defined that Six Sigma requires five stages of implementation which are known as DMAIC method or detailed as Define, Measure, Analyze, Improve and Control [6]. These five stages will be discussed in detail in at the later discussion section.
Failure Mode and Effect Analysis (FMEA)
In the beginning FMEA was developed by Aerospace Industry in the USA on 1960’s, at the 1980’s it was used by Ford company, a famous automotive industry, until the year of 1993, AIAG (Automatic Industry Action Group) and ASQC (American Society for Quality Control) confirmed that FMEA became one of the standard core tools for quality. In the year of 2002, International Organization for Standardization (ISO) included FMEA in their ISO/TS 16949 ‘Technical Specification for Automotive Industry’ as a reference tool [2].
FMEA is one of the methods used by the industry experts to understand and analyze whether a system failure can be measured or analyzed, this theory is to determine whether we can anticipate and mitigate the risk in order to avoid or control the failure. FMEA method when effectively implemented can mitigate the risk, avoiding or minimizing the failure or mistakes and preventing from total process breakdown or failure.
FMEA principles actually are the development from many improvement principles known before. This is in line with the concept of the Father of Scientific Management, Frederick W. Taylor, who according to Ratnasari (2012), he composed some important scientific management concepts which are known as below [5]. The scientific management development concept is actually aiming that there always be a better way to perform the work or job or assignment and this will mean as continual improvement. Below are some examples of what Taylor highlighted in his theory.
1. Carefully select the workers until all workers are given responsibilities and assignments which fit them.
2. Improve workers or staff education and focus on their development.
3. Build relationship between management and workers.
Methodology
Place and Time of Research
The research was performed at PT XYZ in Batam Island and the time needed to complete the research is for about 3 months, which was starting from the first week of April 2016 up to end of June 2016.
Survey Data
a. Literature and library surveys were done to study how the Six Sigma and FMEA methods can resolve the rising defect rate issues and how they will improve the business performance of the company.
b. Observation and direct interview with the company management team, i.e. to observe how the weld defect rate can be minimized using Six Sigma and FMEA methods implementation.
c. Use of the internet media as additional information to support this research.
Survey Process
The research process is done by performing the calculation of DPMO (Defect Per Million Opportunity) and Sigma value of each defect rate calculation. The implementation of FMEA model is to define the root cause of the problem and to look for the solution and mitigation of each problem which caused the rising of defect rate. After the research process has been done and escalated to decision making using RCA (root cause analysis) method and Cause-Effect Diagram which was done by Senior Welding Engineer or Welding Manager in the formulation of corrective actions to the process.
Organization of PT XYZ
Regarding the company organization function and its chain of command or its main activities or manpower management resources and production management as the production facility, PT XYZ is led by a company Director who is managing all activities of the company and responsible for overall quality aspects.
RESULT AND DISCUSSION
Define Stage
In this define stage we know that the average of total defects which are calculated within each month i.e. from the month of October to November 2015 was 15.5% (see Table 1), while in accordance with the company KPI (Key Performance Indicator) that the acceptable value or total defect percentage is maximum 10%. This high defect rate will have an impact on the customer satisfaction which will be indicated by the company receiving more customer complaints and company start suffering budget restraint due to repair works cost and overspent man hours. All this if not resolved will lead to a substantial loss in profit margins. Therefore, the cost of poor quality (COPQ) will be high and will significantly impact the company revenue.
In this defining stage it was recorded that weld defect rate calculated on average during the month of October and November 2015 is 15,5 % (see Table 1), while according to company KPI target the maximum defect rate is 10%. The impact which is occurring from this high repair rate will affect the company satisfaction and invited customer complaints and compelling request of immediate corrective actions and mitigation to this quality problem. Besides the rise of customer complaints or customer dissatisfactions, this high defect rate problem also gave concerns on the repair cost or production re-works cost or known as the cost of poor quality (COPQ). This COPQ will include not only cost of re-works or repairs but also includes the investment of new machines or tools, training cost, etc.
Table 1. Welding Defect Proportion
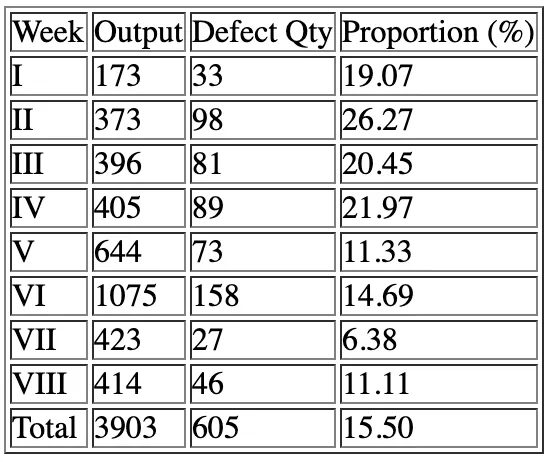
Measure Stage
In this measure stage, some analysis has been done to determine the current process condition or current baseline before the Six Sigma improvement methodology is used. This stage is to define the critical to quality (CTQ) aspects and to measure the product performance by calculation the DPMO, which is to calculate how many defects occurred during a period of production and convert them into DPMO and Sigma level values. The previous research data had shown that the average Sigma level during that stage was Sigma 3.32 (see Table 2). This condition is still far from what the company expected which is to achieve minimum Sigma level of 4.0. In the below table we can see the condition of Sigma level during that periods.
Table 2. Sigma Level Calculation
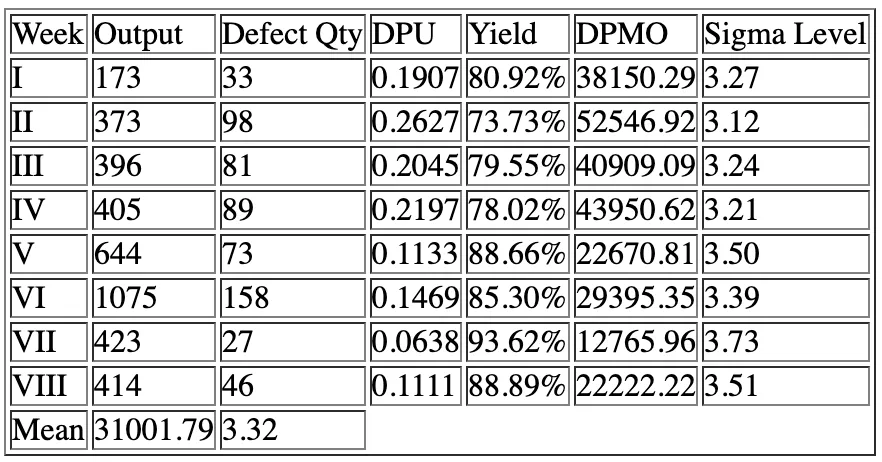
Analyze Stage
Analyze stage is the next hierarchy stage which is also called as the measurement stage. In this stage, the writer is analyzing and identifying the problems which caused the problems to happen. Finding the right problem causes will help us getting the right solutions to the problems and the understanding of the precise root cause will help the company to perform the corrective actions and to prevent the same problems to happen in the future. There are some methods which can be used to analyze the root cause, e.g.:
a. Pareto Chart Analysis
This chart will help the researcher to record and analyze the information of what causing the problems. From the below diagram it can be identified that the highest defect numbers fell on the slag defects, which is a defect caused by improper cleaning and entrapped foreign objects or materials into the weld pool. From the below Pareto analysis, which was recorded before the company performed any improvement or corrective action, we can see the proportions of defects which contributed to the high defect rate problems.
Figure 3. Pareto Chart – Type of Defects
b. Cause-Effect Diagram
This diagram below shows what will be the correlation between the problems or if there is any common factor that simultaneously affects the product or process. Below are some factors which may influence the weld product quality or factors that if studied carefully can improve the current weld quality and remove the undermining problem. Below are some factors which influence the current problems in welds and when it is drawn nicely will give us the fish-bone-like graphics or diagram (see picture 4) below are:
1. Man
2. Material
3. Machine
4. Method
5. Environment
Figure 4. Cause-Effect Diagram
c. 5W-1H Analysis
This concept is used to determine what will be the solution to the weld defects which occur during welding or production. 5W-1H method or analysis can be seen at the below table:
Table 3. 5W-1H Analysis
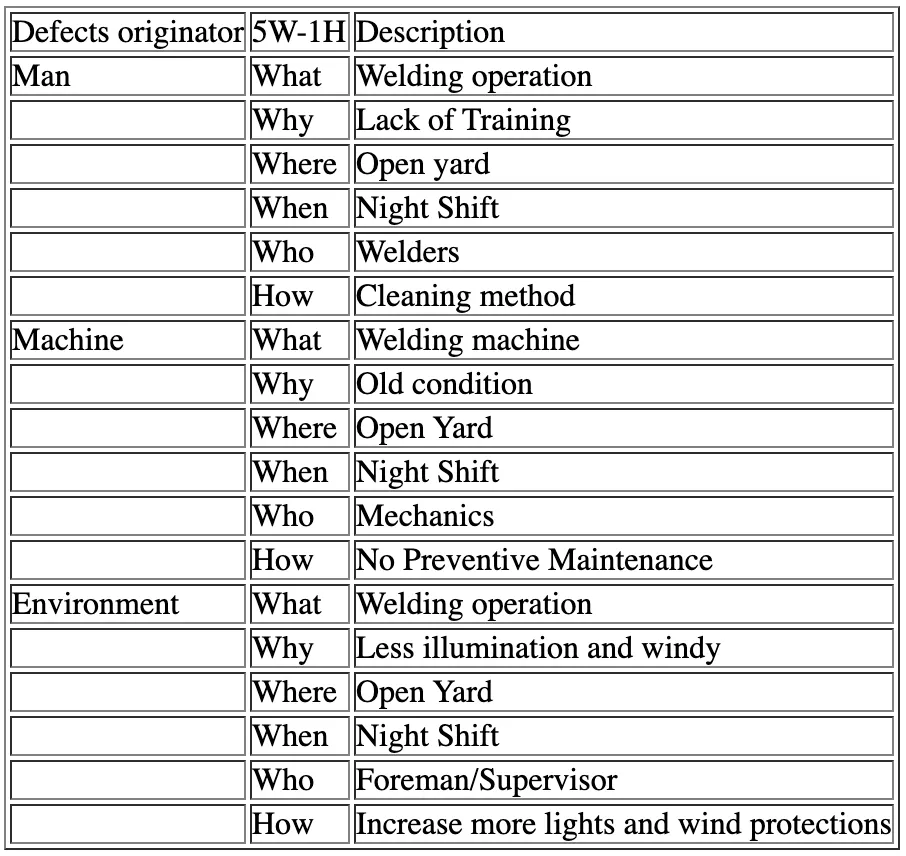
d. FMEA Analysis
This analysis is a method used to understand or observe whether a failure can be analyzed or measured and being anticipated or minimized whether its failure rate of its negative effect on other factors or its process output. Actually, there is a similarity between FMEA and cause-effect diagram which was discussed previously when finding the root cause of a problem, however, with FMEA we can prioritize which problems that are more significant. FMEA gives us three criteria to each problem to be analyzed, those criteria are Severity (S), Occurrence (O), and Detection (D). These three criteria will form a value which is called as Risk Priority Number (RPN), and by using the formula S x O x D = RPN, and now we can give priority which problem will require immediate action due to its high risk. The higher its RPN is the higher its risk and the higher is its urgency to be resolved. Below are some details of each criterion which forms the RPN:
1. Severity (S)
This criterion shows how severe is a problem and how this will affect the product or process quality. This criterion sometimes ranks from 1 to 10, where 1 represents the lighter one and 10 represents the heavier or the worst one.
2. Occurrence (O)
This shows how often is the occurrence of the problem in the production or process. This criterion also is normally ranked from 1 to 10, where 1 represents the hard occurrence and 10 is very often occurrence.
3. Detection (D)
This criterion shows how easy is an incident can be detected before or after it happens during production or process. The criteria are also ranked from 1 to 10, where 1 is the easiest to detect and 10 is the hardest to detect.
Below is the FMEA analysis (Figure 4) which was developed by the company to perform the analysis in resolving the high defect rate issues in its weld production section or unit.
Figure 4. FMEA Analysis
Improve Stage
Improvement stage is performed by implementing all the analysis and methods prescribed in this paper i.e. Pareto analysis, cause-effect diagram, 5W-1H concept and FMEA analysis. After all the plans and strategies are implemented then we can measure that all Sigma level average values are improving, this will be shown in the below table (see Table 4).
Table 4. Calculation of Sigma Level after Rectification

Control Stage
This stage or activity is the final operational stage in improving the quality of products in conjunction with the implementation of Six Sigma and FMEA methods on the production of products or services. At this stage, all the quality records and reports are distributed to relevant parties to be evaluated if the actions taken are meeting with the requirements and give results. This stage also includes documenting all procedures and records for future review or study and for the benefits for future training.
Conclusion
The conclusion which can be made from this paper is that the writer proposes some inputs to the company in order to tackle with the facing problems, which are as below:
- By using Six Sigma and FMEA methods the company can grow more acceptable outputs, achieving the quality objectives, deliver the products on time, and improving the lead time.
- Using these two methods above the company can achieve its periodic KPI, especially when its in-process inspection during production welding can achieve the proposed target of maximum 10% defect rate or repair.
- Using this technique also the company can minimize the cost of poor quality (COPQ) and this also will be in line with the escalation of company profits or values and make the product price more competitive.
- This method also encourages the implementation of quality improvement and develop quality perception amongst customers. These methods are also giving company assurance that the products are well guaranteed.
- The implementation of this paper can improve company image and fulfill the company mission and vision, as the most leading global fabrication company.
References
[1] Montgomery, D.C. 2009. Introduction to Statistical Quality Control. USA. John Wiley &Sons.[2] McDermott, R.E., Mikulak, R.J. &Beuregard, M.R. 2009. The Basics of FMEA. USA. Productivity Press Group.[3] Pande, S.P., Neuman, R.P. &Cavanagh, R.R. 2003. The Six Sigma Way. Yogyakarta. Andi.[4] Ratnasari, S.L. Pengaruh Kompetensi dan Kompensasi Terhadap Kinerja Karyawan Departemen Quality Assurance PT. PEB Batam. Batam. Fakultas Ekonomi Universitas Batam.[5] Ratnasari, S.L. 2012. Frank B. Gilberth, Lillian M. Gilberth dan Perkembangan Ilmu Manajemen. Surabaya. UPN Press. [6] Syukron, A &Kholil, M. 2013. Six Sigma – Quality for Business Improvement. Yogyakarta. Graha Ilmu.
The Open Worldwide Application Security Project (OWASP) is a community-led organization and has been around for over 20 years and is largely known for its Top 10 web application security risks (check out our course on it). As the use of generative AI and large language models (LLMs) has exploded recently, so too has the risk to privacy and security by these technologies. OWASP, leading the charge for security, has come out with its Top 10 for LLMs and Generative AI Apps this year. In this blog post we’ll explore the Top 10 risks and explore examples of each as well as how to prevent these risks.
LLM01: Prompt Injection
Those familiar with the OWASP Top 10 for web applications have seen the injection category before at the top of the list for many years. This is no exception with LLMs and ranks as number one. Prompt Injection can be a critical vulnerability in LLMs where an attacker manipulates the model through crafted inputs, leading it to execute unintended actions. This can result in unauthorized access, data exfiltration, or social engineering. There are two types: Direct Prompt Injection, which involves "jailbreaking" the system by altering or revealing underlying system prompts, giving an attacker access to backend systems or sensitive data, and Indirect Prompt Injection, where external inputs (like files or web content) are used to manipulate the LLM's behavior.
As an example, an attacker might upload a resume containing an indirect prompt injection, instructing an LLM-based hiring tool to favorably evaluate the resume. When an internal user runs the document through the LLM for summarization, the embedded prompt makes the LLM respond positively about the candidate’s suitability, regardless of the actual content.
How to prevent prompt injection:
- Limit LLM Access: Apply the principle of least privilege by restricting the LLM's access to sensitive backend systems and enforcing API token controls for extended functionalities like plugins.
- Human Approval for Critical Actions: For high-risk operations, require human validation before executing, ensuring that the LLM's suggestions are not followed blindly.
- Separate External and User Content: Use frameworks like ChatML for OpenAI API calls to clearly differentiate between user prompts and untrusted external content, reducing the chance of unintentional action from mixed inputs.
- Monitor and Flag Untrusted Outputs: Regularly review LLM outputs and mark suspicious content, helping users to recognize potentially unreliable information.
LLM02: Insecure Output Handling
Insecure Output Handling occurs when the outputs generated by a LLM are not properly validated or sanitized before being used by other components in a system. Since LLMs can generate various types of content based on input prompts, failing to handle these outputs securely can introduce risks like cross-site scripting (XSS), server-side request forgery (SSRF), or even remote code execution (RCE). Unlike Overreliance (LLM09), which focuses on the accuracy of LLM outputs, Insecure Output Handling specifically addresses vulnerabilities in how these outputs are processed downstream.
As an example, there could be a web application that uses an LLM to summarize user-provided content and renders it back in a webpage. An attacker submits a prompt containing malicious JavaScript code. If the LLM’s output is displayed on the webpage without proper sanitization, the JavaScript will execute in the user’s browser, leading to XSS. Alternatively, if the LLM’s output is sent to a backend database or shell command, it could allow SQL injection or remote code execution if not properly validated.
How to prevent Insecure Output Handling:
- Zero-Trust Approach: Treat the LLM as an untrusted source, applying strict allow list validation and sanitization to all outputs it generates, especially before passing them to downstream systems or functions.
- Output Encoding: Encode LLM outputs before displaying them to end users, particularly when dealing with web content where XSS risks are prevalent.
- Adhere to Security Standards: Follow the OWASP Application Security Verification Standard (ASVS) guidelines, which provide strategies for input validation and sanitization to protect against code injection risks.
LLM03: Training Data Poisoning
Training Data Poisoning refers to the manipulation of the data used to train LLMs, introducing biases, backdoors, or vulnerabilities. This tampered data can degrade the model's effectiveness, introduce harmful biases, or create security flaws that malicious actors can exploit. Poisoned data could lead to inaccurate or inappropriate outputs, compromising user trust, harming brand reputation, and increasing security risks like downstream exploitation.
As an example, there could be a scenario where an LLM is trained on a dataset that has been tampered with by a malicious actor. The poisoned dataset includes subtly manipulated content, such as biased news articles or fabricated facts. When the model is deployed, it may output biased information or incorrect details based on the poisoned data. This not only degrades the model’s performance but can also mislead users, potentially harming the model’s credibility and the organization’s reputation.
How to prevent Training Data Poisoning:
- Data Validation and Vetting: Verify the sources of training data, especially when sourcing from third-party datasets. Conduct thorough checks on data integrity, and where possible, use trusted data sources.
- Machine Learning Bill of Materials (ML-BOM): Maintain an ML-BOM to track the provenance of training data and ensure that each source is legitimate and suitable for the model’s purpose.
- Sandboxing and Network Controls: Restrict access to external data sources and use network controls to prevent unintended data scraping during training. This helps ensure that only vetted data is used for training.
- Adversarial Robustness Techniques: Implement strategies like federated learning and statistical outlier detection to reduce the impact of poisoned data. Periodic testing and monitoring can identify unusual model behaviors that may indicate a poisoning attempt.
- Human Review and Auditing: Regularly audit model outputs and use a human-in-the-loop approach to validate outputs, especially for sensitive applications. This added layer of scrutiny can catch potential issues early.
LLM04: Model Denial of Service
Model Denial of Service (DoS) is a vulnerability in which an attacker deliberately consumes an excessive amount of computational resources by interacting with a LLM. This can result in degraded service quality, increased costs, or even system crashes. One emerging concern is manipulating the context window of the LLM, which refers to the maximum amount of text the model can process at once. This makes it possible to overwhelm the LLM by exceeding or exploiting this limit, leading to resource exhaustion.
As an example, an attacker may continuously flood the LLM with sequential inputs that each reach the upper limit of the model’s context window. This high-volume, resource-intensive traffic overloads the system, resulting in slower response times and even denial of service. As another example, if an LLM-based chatbot is inundated with a flood of recursive or exceptionally long prompts, it can strain computational resources, causing system crashes or significant delays for other users.
How to prevent Model Denial of Service:
- Rate Limiting: Implement rate limits to restrict the number of requests from a single user or IP address within a specific timeframe. This reduces the chance of overwhelming the system with excessive traffic.
- Resource Allocation Caps: Set caps on resource usage per request to ensure that complex or high-resource requests do not consume excessive CPU or memory. This helps prevent resource exhaustion.
- Input Size Restrictions: Limit input size according to the LLM's context window capacity to prevent excessive context expansion. For example, inputs exceeding a predefined character limit can be truncated or rejected.
- Monitoring and Alerts: Continuously monitor resource utilization and establish alerts for unusual spikes, which may indicate a DoS attempt. This allows for proactive threat detection and response.
- Developer Awareness and Training: Educate developers about DoS vulnerabilities in LLMs and establish guidelines for secure model deployment. Understanding these risks enables teams to implement preventative measures more effectively.
LLM05: Supply Chain Vulnerabilities
Supply Chain attacks are incredibly common and this is no different with LLMs, which, in this case refers to risks associated with the third-party components, training data, pre-trained models, and deployment platforms used within LLMs. These vulnerabilities can arise from outdated libraries, tampered models, and even compromised data sources, impacting the security and reliability of the entire application. Unlike traditional software supply chain risks, LLM supply chain vulnerabilities extend to the models and datasets themselves, which may be manipulated to include biases, backdoors, or malware that compromises system integrity.
As an example, an organization uses a third-party pre-trained model to conduct economic analysis. If this model is poisoned with incorrect or biased data, it could generate inaccurate results that mislead decision-making. Additionally, if the organization uses an outdated plugin or compromised library, an attacker could exploit this vulnerability to gain unauthorized access or tamper with sensitive information. Such vulnerabilities can result in significant security breaches, financial loss, or reputational damage.
How to prevent Supply Chain Vulnerabilities:
- Vet Third-Party Components: Carefully review the terms, privacy policies, and security measures of all third-party model providers, data sources, and plugins. Use only trusted suppliers and ensure they have robust security protocols in place.
- Maintain a Software Bill of Materials (SBOM): An SBOM provides a complete inventory of all components, allowing for quick detection of vulnerabilities and unauthorized changes. Ensure that all components are up-to-date and apply patches as needed.
- Use Model and Code Signing: For models and external code, employ digital signatures to verify their integrity and authenticity before use. This helps ensure that no tampering has occurred.
- Anomaly Detection and Robustness Testing: Conduct adversarial robustness tests and anomaly detection on models and data to catch signs of tampering or data poisoning. Integrating these checks into your MLOps pipeline can enhance overall security.
- Implement Monitoring and Patching Policies: Regularly monitor component usage, scan for vulnerabilities, and patch outdated components. For sensitive applications, continuously audit your suppliers’ security posture and update components as new threats emerge.
LLM06: Sensitive Information Disclosure
Sensitive Information Disclosure in LLMs occurs when the model inadvertently reveals private, proprietary, or confidential information through its output. This can happen due to the model being trained on sensitive data or because it memorizes and later reproduces private information. Such disclosures can result in significant security breaches, including unauthorized access to personal data, intellectual property leaks, and violations of privacy laws.
As an example, there could be an LLM-based chatbot trained on a dataset containing personal information such as users’ full names, addresses, or proprietary business data. If the model memorizes this data, it could accidentally reveal this sensitive information to other users. For instance, a user might ask the chatbot for a recommendation, and the model could inadvertently respond with personal information it learned during training, violating privacy rules.
How to prevent Sensitive Information Disclosure:
- Data Sanitization: Before training, scrub datasets of personal or sensitive information. Use techniques like anonymization and redaction to ensure no sensitive data remains in the training data.
- Input and Output Filtering: Implement robust input validation and sanitization to prevent sensitive data from entering the model’s training data or being echoed back in outputs.
- Limit Training Data Exposure: Apply the principle of least privilege by restricting sensitive data from being part of the training dataset. Fine-tune the model with only the data necessary for its task, and ensure high-privilege data is not accessible to lower-privilege users.
- User Awareness: Make users aware of how their data is processed by providing clear Terms of Use and offering opt-out options for having their data used in model training.
- Access Controls: Apply strict access control to external data sources used by the LLM, ensuring that sensitive information is handled securely throughout the system
LLM07: Insecure Plugin Design
Insecure Plugin Design vulnerabilities arise when LLM plugins, which extend the model’s capabilities, are not adequately secured. These plugins often allow free-text inputs and may lack proper input validation and access controls. When enabled, plugins can execute various tasks based on the LLM’s outputs without further checks, which can expose the system to risks like data exfiltration, remote code execution, and privilege escalation. This vulnerability is particularly dangerous because plugins can operate with elevated permissions while assuming that user inputs are trustworthy.
As an example, there could be a weather plugin that allows users to input a base URL and query. An attacker could craft a malicious input that directs the LLM to a domain they control, allowing them to inject harmful content into the system. Similarly, a plugin that accepts SQL “WHERE” clauses without validation could enable an attacker to execute SQL injection attacks, gaining unauthorized access to data in a database.
How to prevent Insecure Plugin Design:
- Enforce Parameterized Input: Plugins should restrict inputs to specific parameters and avoid free-form text wherever possible. This can prevent injection attacks and other exploits.
- Input Validation and Sanitization: Plugins should include robust validation on all inputs. Using Static Application Security Testing (SAST) and Dynamic Application Security Testing (DAST) can help identify vulnerabilities during development.
- Access Control: Follow the principle of least privilege, limiting each plugin's permissions to only what is necessary. Implement OAuth2 or API keys to control access and ensure only authorized users or components can trigger sensitive actions.
- Manual Authorization for Sensitive Actions: For actions that could impact user security, such as transferring files or accessing private repositories, require explicit user confirmation.
- Adhere to OWASP API Security Guidelines: Since plugins often function as REST APIs, apply best practices from the OWASP API Security Top 10. This includes securing endpoints and applying rate limiting to mitigate potential abuse.
LLM08: Excessive Agency
Excessive Agency in LLM-based applications arises when models are granted too much autonomy or functionality, allowing them to perform actions beyond their intended scope. This vulnerability occurs when an LLM agent has access to functions that are unnecessary for its purpose or operates with excessive permissions, such as being able to modify or delete records instead of only reading them. Unlike Insecure Output Handling, which deals with the lack of validation on the model’s outputs, Excessive Agency pertains to the risks involved when an LLM takes actions without proper authorization, potentially leading to confidentiality, integrity, and availability issues.
As an example, there could be an LLM-based assistant that is given access to a user's email account to summarize incoming messages. If the plugin that is used to read emails also has permissions to send messages, a malicious prompt injection could trick the LLM into sending unauthorized emails (or spam) from the user's account.
How to prevent Excessive Agency:
- Restrict Plugin Functionality: Ensure plugins and tools only provide necessary functions. For example, if a plugin is used to read emails, it should not include capabilities to delete or send emails.
- Limit Permissions: Follow the principle of least privilege by restricting plugins’ access to external systems. For instance, a plugin for database access should be read-only if writing or modifying data is not required.
- Avoid Open-Ended Functions: Avoid functions like “run shell command” or “fetch URL” that provide broad system access. Instead, use plugins that perform specific, controlled tasks.
- User Authorization and Scope Tracking: Require plugins to execute actions within the context of a specific user's permissions. For example, using OAuth with limited scopes helps ensure actions align with the user’s access level.
- Human-in-the-Loop Control: Require user confirmation for high-impact actions. For instance, a plugin that posts to social media should require the user to review and approve the content before it is published.
- Authorization in Downstream Systems: Implement authorization checks in downstream systems that validate each request against security policies. This prevents the LLM from making unauthorized changes directly.
LLM09: Overreliance
Overreliance occurs when users or systems trust the outputs of a LLM without proper oversight or verification. While LLMs can generate creative and informative content, they are prone to “hallucinations” (producing false or misleading information) or providing authoritative-sounding but incorrect outputs. Overreliance on these models can result in security risks, misinformation, miscommunication, and even legal issues, especially if LLM-generated content is used without validation. This vulnerability becomes especially dangerous in cases where LLMs suggest insecure coding practices or flawed recommendations.
As an example, there could be a development team using an LLM to expedite the coding process. The LLM suggests an insecure code library, and the team, trusting the LLM, incorporates it into their software without review. This introduces a serious vulnerability. As another example, a news organization might use an LLM to generate articles, but if they don’t validate the information, it could lead to the spread of disinformation.
How to prevent Overreliance:
- Regular Monitoring and Review: Implement processes to review LLM outputs regularly. Use techniques like self-consistency checks or voting mechanisms to compare multiple model responses and filter out inconsistencies.
- Cross-Verification: Compare the LLM’s output with reliable, trusted sources to ensure the information’s accuracy. This step is crucial, especially in fields where factual accuracy is imperative.
- Fine-Tuning and Prompt Engineering: Fine-tune models for specific tasks or domains to reduce hallucinations. Techniques like parameter-efficient tuning (PET) and chain-of-thought prompting can help improve the quality of LLM outputs.
- Automated Validation: Use automated validation tools to cross-check generated outputs against known facts or data, adding an extra layer of security.
- Risk Communication: Clearly communicate the limitations of LLMs to users, highlighting the potential for errors. Transparent disclaimers can help manage user expectations and encourage cautious use of LLM outputs.
- Secure Coding Practices: For development environments, establish guidelines to prevent the integration of potentially insecure code. Avoid relying solely on LLM-generated code without thorough review.
LLM10: Model Theft
Model Theft refers to the unauthorized access, extraction, or replication of proprietary LLMs by malicious actors. These models, containing valuable intellectual property, are at risk of exfiltration, which can lead to significant economic and reputational loss, erosion of competitive advantage, and unauthorized access to sensitive information encoded within the model. Attackers may steal models directly from company infrastructure or replicate them by querying APIs to build shadow models that mimic the original. As LLMs become more prevalent, safeguarding their confidentiality and integrity is crucial.
As an example, an attacker could exploit a misconfiguration in a company’s network security settings, gaining access to their LLM model repository. Once inside, the attacker could exfiltrate the proprietary model and use it to build a competing service. Alternatively, an insider may leak model artifacts, allowing adversaries to launch gray box adversarial attacks or fine-tune their own models with stolen data.
How to prevent Model Theft:
- Access Controls and Authentication: Use Role-Based Access Control (RBAC) and enforce strong authentication mechanisms to limit unauthorized access to LLM repositories and training environments. Adhere to the principle of least privilege for all user accounts.
- Supplier and Dependency Management: Monitor and verify the security of suppliers and dependencies to reduce the risk of supply chain attacks, ensuring that third-party components are secure.
- Centralized Model Inventory: Maintain a central ML Model Registry with access controls, logging, and authentication for all production models. This can aid in governance, compliance, and prompt detection of unauthorized activities.
- Network Restrictions: Limit LLM access to internal services, APIs, and network resources. This reduces the attack surface for side-channel attacks or unauthorized model access.
- Continuous Monitoring and Logging: Regularly monitor access logs for unusual activity and promptly address any unauthorized access. Automated governance workflows can also help streamline access and deployment controls.
- Adversarial Robustness: Implement adversarial robustness training to help detect extraction queries and defend against side-channel attacks. Rate-limit API calls to further protect against data exfiltration.
- Watermarking Techniques: Embed unique watermarks within the model to track unauthorized copies or detect theft during the model’s lifecycle.
Wrapping it all up
As LLMs continue to grow in capability and integration across industries, their security risks must be managed with the same vigilance as any other critical system. From Prompt Injection to Model Theft, the vulnerabilities outlined in the OWASP Top 10 for LLMs highlight the unique challenges posed by these models, particularly when they are granted excessive agency or have access to sensitive data. Addressing these risks requires a multifaceted approach involving strict access controls, robust validation processes, continuous monitoring, and proactive governance.
For technical leadership, this means ensuring that development and operational teams implement best practices across the LLM lifecycle starting from securing training data to ensuring safe interaction between LLMs and external systems through plugins and APIs. Prioritizing security frameworks such as the OWASP ASVS, adopting MLOps best practices, and maintaining vigilance over supply chains and insider threats are key steps to safeguarding LLM deployments. Ultimately, strong leadership that emphasizes security-first practices will protect both intellectual property and organizational integrity, while fostering trust in the use of AI technologies.